Manually building pallets that contain different, or mixed, stock keeping units (SKUs) is one of the most physically taxing jobs in a warehouse. When the products are sold in bulk quantities ranging from 10 to 50 pounds — and packaged in bags — the physical and ergonomic demands on warehouse associates can be grueling.
Yet, for many distribution centers (DCs) replenishing brick-and-mortar retail stores, it’s a common scenario. Think dog food, flour, and sugar in grocery stores. Or leveling sand, potting mix, mulch, and fertilizer at home improvement outlets. These are all heavy, bulky, and capable of making an enormous mess if the bag is damaged. Further, and they also have to be palletized in a specific sequence to match the store’s planogram for easy restocking of shelves.
Given all those factors, automating mixed bag palletizing for retail replenishment is a great idea. It’s also something that operations managers would love to do successfully — but has been challenging to execute. Although conventional palletizing automation and multi-axis robotic palletizing have been in use to create loads of cartons for two decades, building a mixed pallet consisting of a variety of product dimensions, weights, shapes, and contents is much more difficult to automate.
That’s why DCS shared an innovative, automated palletizing solution engineered for handling mixed bags in an educational session at MODEX. Here’s an overview of “Getting the Business Case Right in Automated Mixed SKU Pallet Fulfillment.”
DCS Combines Software, Automation, AI to Automate Mixed Bag Palletizing
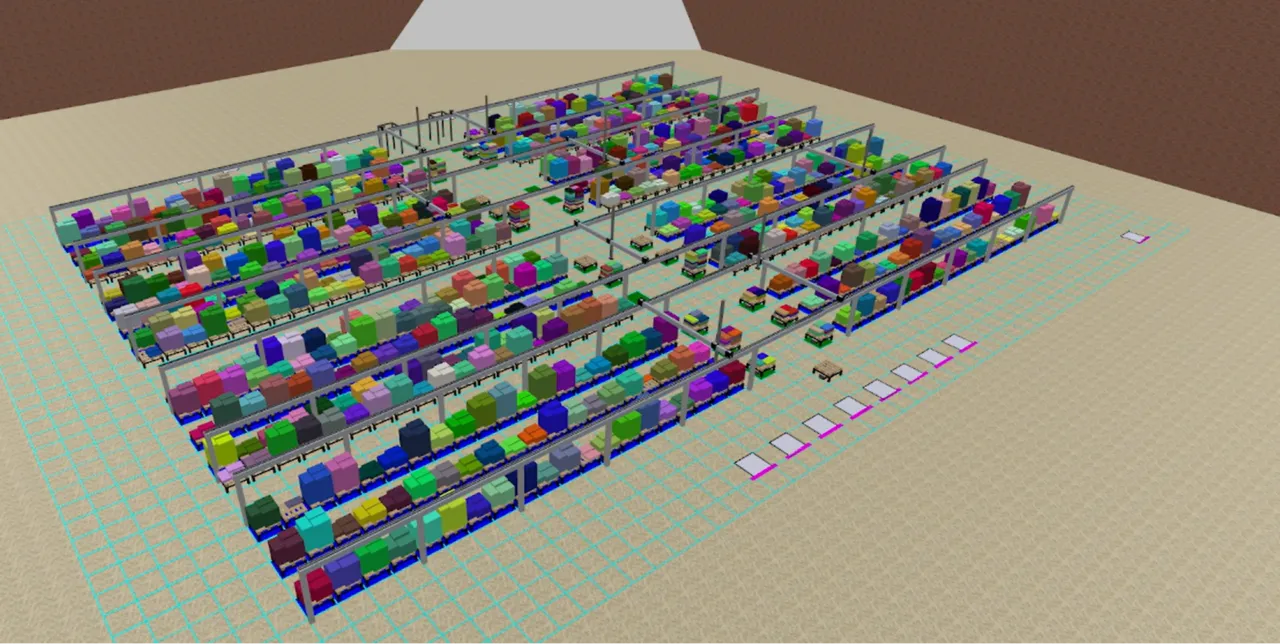
The session, walked through the layout pictured above. This automated palletizing solution combines multiple proven technologies. They include:
In this operation, all source inventory pallets and outbound pallets each sit on low racks. The AMRs tunnel under the racks to lift them slightly up off the floor, then transport them where needed. Source inventory sits in rows within eight separate work cells, each equipped with a gantry crane.
The work cells are arranged four on either side of a central aisle where outbound pallets are staged. Each crane has a robotic arm with vacuum end effectors and an integrated vision system. As directed by the WES — which orchestrates the entire process — the gantry crane in each work cell travels back and forth over the pallets of inventory.
The on-board vision system detects and reads data tags, as well as identifies the position of each bag on its source pallet to ensure precise pick up. Further, the integrated AI middleware continuously analyzes the data inputs from the vision system. This enables the crane’s robotic arm to make minute adjustments as it places each bag on the outbound mixed pallet (it resembles playing the game Tetris). The system also automatically makes decisions about each bag’s placement based on its dimensions, while simultaneously following the sequential layout of the destination store for easiest restocking.
Once an outbound pallet is picked complete, an AMR tunnels under its rack and transports it to an automatic stretch wrapper to secure the load. The load is then tagged by an automatic print-and-apply labeler. A different AMR delivers an empty pallet to the vacated location, and the process repeats.
Within the work cells, AMRs also remove the racks of empty pallets once picked out and replenish stock for picking. Because it’s controlling the distribution of picks across the eight work cells, the WES also knows when replenishment inventory will be needed. It stays a few waves ahead, staging those pallets in a close by buffer zone, then slotting them into the cells dynamically.
At peak productivity the system creates approximately 28 pallets per hour for store replenishment. Because it is both flexible and scalable, the system could accommodate a variety of inventory slotting schemes of mixed or mirrored inventory per work cell. But, most importantly, no human intervention is required throughout any of these processes. While it isn’t a dark DC, the system automatically builds stable, store ready pallet loads of mixed, bagged products. This allows associates to be reassigned to higher value tasks that are less ergonomically taxing.
Making the Business Case for Automation
This system addresses the primary objective discussed at the outset of this post: the desire to improve warehouse associate safety and retention. In fact, the majority of companies considering these kinds of automation projects are justifying them for reasons outside of achieving a cut-and-dried return on investment (ROI) within a certain time period.
Automated palletizing solutions like this one eliminate actions that pose a higher risk of ergonomic injury due to repetitive motions like bending, lifting, and twisting. Building pallets by hand is a physically demanding job, and one that employees are more likely to quit. Implementing a fully automated solution eliminates an onerous task, as well as the costs associated with workers’ compensation and constant turnover.
Likewise, employee satisfaction at the brick-and-mortar level also increases. Because the pallets are built to match the store layout, the store associates have an easier time restocking shelves. They navigate up and down aisles, unloading the pallet’s contents sequentially — no doubling back required. And the pallet loads themselves are more neatly assembled and better balanced when built by automation than by hand. That makes them easier to guide through narrow store aisles and to unload without fear of subsequent bags sliding off.
Further, the automation moves at a consistent, predictable pace. That, along with its work cell configuration, enhances overall process reliability and uniformity. Guided by integrated vision systems, each gantry crane’s robotic arm and vacuum grippers methodically pick up each bag in the optimal orientation to prevent damage. Wasted merchandise — and the mess that comes with spilled granules, pellets, grains, powders or other bulk products sold by the bag — is significantly reduced.
All of these business case benefits combine to deliver successful automation of mixed load palletizing of bagged goods for retail replenishment using readily available material handling equipment. Achieving this just requires an innovative approach to combining hardware and software in a unique way — something DCS is known for.
Experience DCS’ Approach to Solving Customer Problems
If you’d like to learn more about how DCS can apply an automated solution to successfully address your challenges while making a positive impact on your bottom line, connect with us.